Linear Potentiometers
Potentiometric linear position sensors for distance measurement
Guide Linear Potentiometers
Index
Basic questions about linear sensors? Here you will find the answers
What is a potentiometric linear sensor?
The measuring principle of the potentiometer was already described by Johann Christian Poggendorff in 1841 and has been used since the beginning of the use of electricity. A potentiometer has a resistance track on the surface of which a movable sliding contact is guided which taps a voltage potential. This resistance element can be circular or elongated.
However, the term "potentiometer", or "pot" for short, is most commonly used today for angle sensors, i.e. the round version.
Potentiometric displacement transducers, on the other hand, are sensors used to measure length. These sensors are therefore more likely to be found under the name "linear potentiometers" or the more general term "linear displacement transducers" when a resistance value is specified or when it is obvious that potentiometric technology is involved.
To operate such a sensor, a power supply is connected to the displacement transducer. A wiper is moved on the resistor track by means of a mechanical device (probe, slider, depending on the version), whose potential changes as a result of the displacement: The output voltage at the wiper is proportional to the position of the wiper on the resistor track. The resistor track is made of high-quality conductive plastic, which generates a continuously variable output signal and allows actuation speeds of up to 10 m/sec.
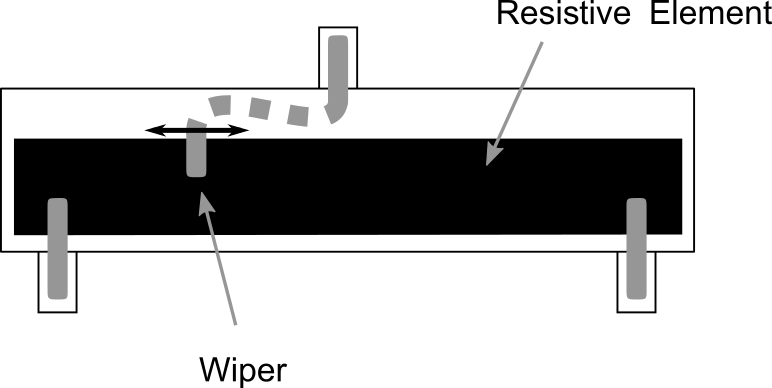
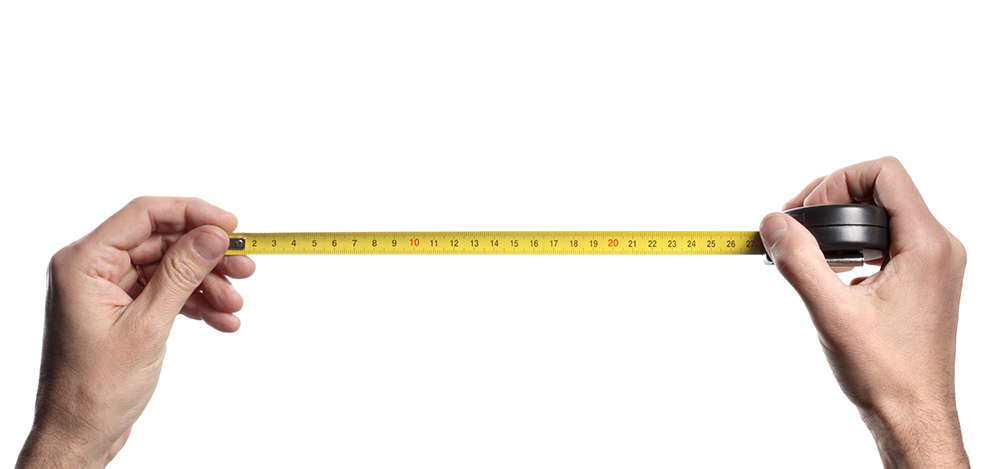
Advantages of linear potentiometers
- The measuring principle is an absolute one, i.e. the same measured value is immediately available when switching on or after a power failure.
- The technology is well proven and easy to handle.
- Only a voltage source with low power is required, because the measured value is taken with low power.
- With potentiometric displacement sensors, displacements in the range from 0 to 10 mm, but also lengths of up to 2000 mm can be measured with a cost-effective sensor and further processed in analogue form.
- Linear potentiometers are very temperature stable in the voltage divider circuit
- Potentiometric displacement transducers are robust against EMC and ESD influences
The following must be observed with linear potentiometers
- We recommend the overhead mounting, so that abrasion does not remain on the resistance element.
- The displacement sensor should not be subjected to excessive vibration, as there is a risk of the slider briefly lifting off the track and interrupting the time curve of the measured value.
- The sensors are not suitable for high vibration applications. High frequency movements at the same point must be avoided at all costs! This will lead to localized abrasion, loss of signal quality on the resistance track and permanent damage to the slider.
- Potentiometric transducers with conductive plastic track must only be used in a voltage divider circuit, as the measured value must be taken at low power. In a rheostat circuit, the conductive plastic track will be permanently damaged. This means that linear potentiometers should not be used as variable resistors in a circuit.
Electrical connection and measurement example
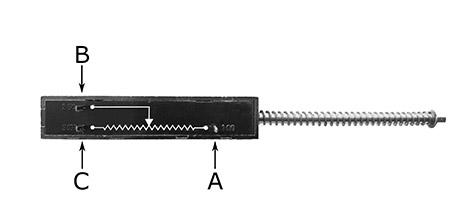
Potentiometric transducers always have three connections as standard, e.g. pins A, B and C. The transducer is supplied with a DC voltage between points A and C. As an example, 10 V is assumed. Terminal A is at 0 V and terminal B is at +10 V. The measurement of the displacement is based on the principle of the voltage divider circuit, i.e. the moving wiper (connected to pin B) has a certain potential relative to the reference point (A), depending on the position of the wiper between the start and end of the resistance track.
For the example shown (simplified):
- If the stroke is at the first end position, the wiper is at the start of the resistance track, so the voltage on pin B is about 0 V.
- The stroke is in the middle, the voltage on B is about 5 V
- The stroke is at the second end position, the wiper is at the end of the resistance track, the voltage at pin B is about +10 V
If the sensors are correctly connected in a voltage divider circuit, the voltage value at point B is independent of the absolute resistance value of the transducer. It should be noted, however, that this illustration is simplified, as different values of electrical and mechanical displacement still apply to the operation of the sensor (see mechanical and electrical travel). Furthermore, no sensor operates without measurement inaccuracy. The deviation of the measurement result from the ideal straight line is specified by the linearity specifications.
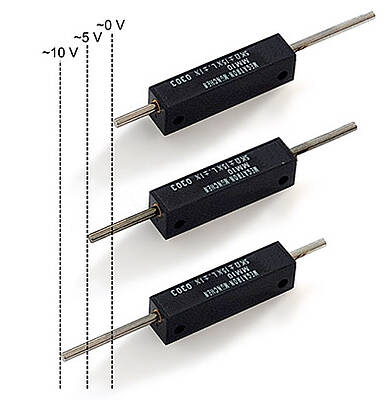
Load capacity of wiper and resistance element
Example | Voltage U | Resistance R | Power P | Application possible? |
1 | 10 V | 1 kΩ | 0.1 Watt | yes |
2 | 20 V | 1 kΩ | 0.4 Watt | no |
3 | 25 V | 5 kΩ | 0.125 Watt | yes |
4 | 60 V | 10 kΩ | 0.36 Watt | no |
5 | 60 V | 20 kΩ | 0.18 Watt | yes |
When connecting, take into account the maximum load capacity of the wiper and resistor element. This information can be found on the relevant data sheet. An excessive current through the wiper will result in immediate destruction of the wiper and/or the resistance track at the current position of the wiper.
The resistance value and the applied voltage are important in determining the power dissipation of the transducer. Here are some calculations using the MM10 transducer as an example:
- max. load capacity 0.2 Watt
- available resistance values 1, 2, 5, 10, 20 or 50 kΩ
The following applies to power dissipation:
P = U² / R (power P = voltage U² divided by resistance R)
From this calculation example it is immediately clear that at an operating voltage of 20 V the 1 kΩ displacement transducer cannot be used because otherwise the power dissipation loaded on the resistive element would be too great.
It is also important to use a very high input impedance when processing the signal in an electronic system, so that the current through the slider (pin B) is as low as possible. The voltage difference between pin B and pin A is measured to record the measurements.
Mechanical and electrical travel
The output characteristic curve of most potentiometric displacement sensors is not suitable for sensor operation over the entire available displacement range. A basic distinction must be made between the following displacement ranges:
- Effective electrical limits: This is the actual travel to be used for the measurement. The linearity values specified in the data sheet apply to this travel and continuous operation should only take place within these limits.
- Total electrical limits: Within this range the wiper provides an output signal, but this signal usually does not change at the ends of the travel, but remains constant. This is a kind of "dead zone", which is designed in this way for technical or design reasons and is not available with all sensors.
- Mechanical limits: The actual displacement that the position sensor can perform. On most models, mechanical stops prevent the slider from moving beyond the resistance path.
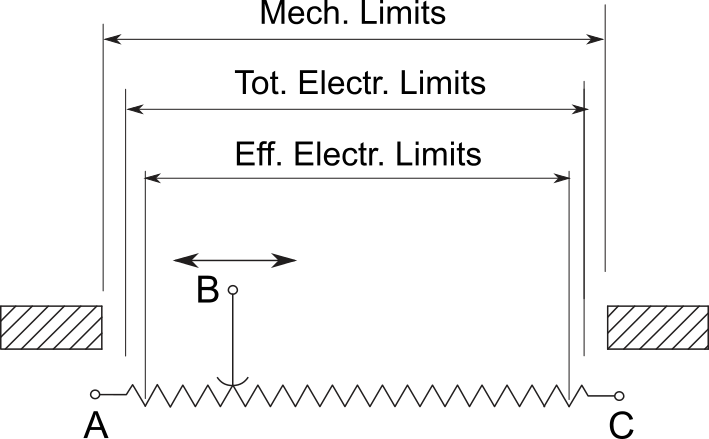
For many models, the mechanical travel is the same as the full electrical travel. This leaves only two of the three ranges described above. Although this simplifies the consideration, the effective electrical travel must still be adjusted to the application when installing the sensor. Otherwise, the dead range described above will falsify the measurement results. Please refer to the data sheet for the model you have chosen.
Oil-filled transducers
Oil-filled potentiometric displacement sensors are available for applications with special requirements for sensor durability. They are particularly suitable for measuring points in dirty, damp or even corrosive environments (salts, corrosive gases). Applications for these sensors can be found in heavy industries such as shipbuilding, mines, steelworks, chemical plants and many more.
The simplest way to convert a linear movement into a proportional electrical quantity is still to use potentiometric measuring systems. These are absolute measuring systems with a resolution of better than 0.01 mm and the well-known advantage that the signals are immediately displayed in the correct position if the power supply fails. Our linear potentiometers cover mechanical stroke lengths up to 2000 mm.
Whether as probe with spring return, with ball joints to compensate lateral misalignment, as slide-guided version or for installation in hydraulic applications, they all have a very high quality conductive plastic resistive element (except the oil-filled with wirewound element). And despite the variety and diversity of the products, some demanding applications require sensor customization.
We at MEGATRON are your partner in this adaptation process and will support you from product selection through to the end of the life cycle of your application. Potentiometric sensors, in particular, often require special adaptations of the measuring paths, the assemblies and improvements in the precision of the components, because in demanding special applications, such as in medical technology, the standard variants often do not meet all the requirements.